Metal Stamping: Advancements Driving Industry Growth
Metal Stamping: Advancements Driving Industry Growth
Blog Article
Unlocking the Power of Metal Stamping: Strategies for Boosted Item Advancement
In the realm of production, the use of steel marking holds a substantial place as a result of its adaptability and efficiency in producing complex components and parts. The true capacity of metal stamping stays untapped by lots of business seeking to improve their product development procedures. By discovering sophisticated strategies and methods customized to optimize design, product option, production effectiveness, and quality assurance, companies can open a riches of chances to boost their products to new heights of development and performance.
Advantages of Metal Stamping
Metal stamping deals a effective and economical technique for generating top notch metal elements. One of the vital advantages of metal marking is its capacity to produce intricate geometries with high precision and consistency.
Additionally, metal stamping permits for high-volume manufacturing, making it suitable for tasks that call for large amounts of steel components. The rate and repeatability of the marking procedure not only ensure price savings yet additionally contribute to faster turn-around times for production orders. In addition, using computerized devices in steel marking helps reduce the threat of human mistake, leading to boosted total product top quality.
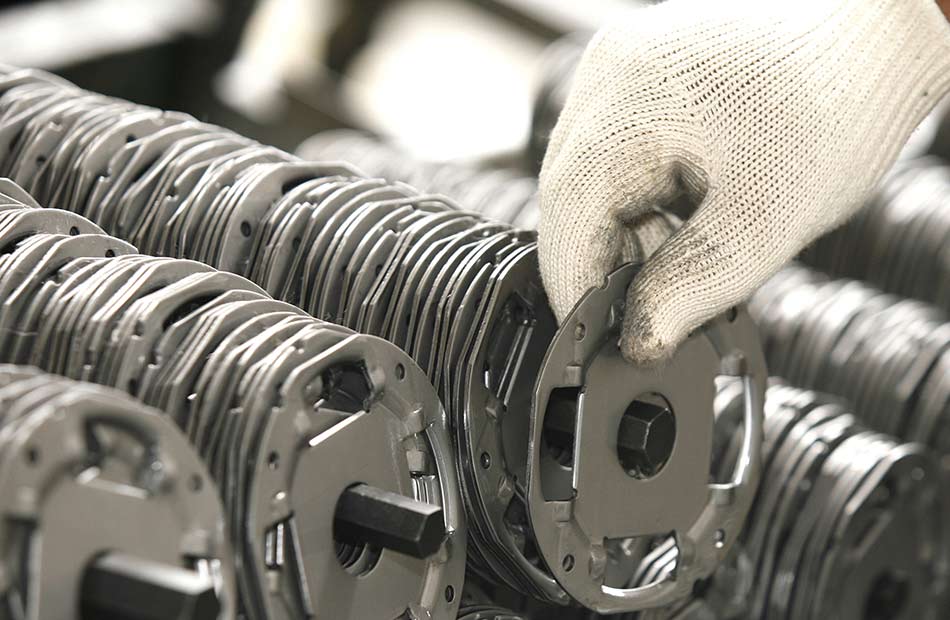
Design Optimization Techniques
With mindful consideration of product homes and geometric configurations, style optimization techniques play a vital duty in enhancing the efficiency and functionality of steel stamping procedures. By purposefully analyzing variables such as material type, thickness, and stamina, suppliers can tailor the style to make the most of the efficiency of the marking procedure. Making use of simulation software, designers can anticipate just how different design variants will act under numerous stamping problems, permitting for the identification of potential issues prior to manufacturing begins.
Additionally, integrating functions like fillets, chamfers, and embosses right into the design can boost the overall quality of the stamped part while decreasing the risk of defects such as cracking or deforming. In addition, maximizing the format of functions on the part can improve the material flow throughout marking, leading to more precise and constant outcomes.
In significance, design optimization strategies enable suppliers to tweak their steel marking procedures, causing enhanced product top quality, increased manufacturing performance, and inevitably, a more competitive setting in the market.
Material Option Techniques
Style optimization strategies in metal marking processes heavily rely upon strategic product option techniques to guarantee the wanted performance and effectiveness of the made parts. The option of material in metal marking is crucial as it directly affects the quality, resilience, and total functionality of the end product. When choosing the ideal product for a certain project, variables such as mechanical residential properties, formability, cost-effectiveness, and deterioration resistance need to be considered.
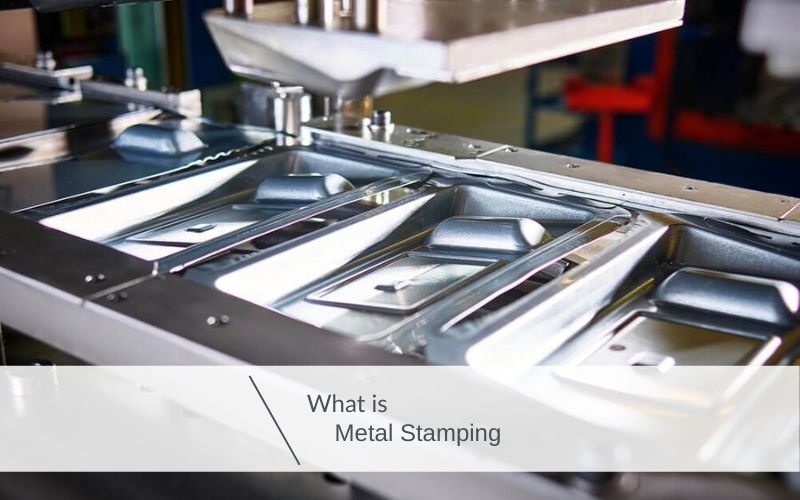
Additionally, cost-effectiveness plays a significant duty in product choice strategies. Stabilizing the performance needs with the general cost of materials is essential to guarantee the economic practicality of the manufacturing procedure. Furthermore, considering factors like recyclability and environmental influence can better boost the sustainability of the selected product. By thoroughly reviewing these facets, producers can optimize their product option approaches to achieve premium try these out product high quality and functional efficiency.
Enhancing Production Efficiency
Effectiveness in production processes is a critical factor for ensuring cost-effectiveness and timely distribution of top notch steel stamped parts. To improve production efficiency in metal marking, a number of methods can be carried out.
Additionally, executing automation and robotics in steel marking operations can significantly enhance performance and uniformity while lowering labor prices. Automated systems can execute repetitive tasks with high accuracy and speed, bring about enhanced production effectiveness and higher outcome rates. Buying modern stamping tools with sophisticated attributes, such as servo-driven presses and quick die modification systems, browse this site can additionally enhance manufacturing processes and decrease downtime.
Moreover, developing clear communication channels and promoting collaboration in between design, layout, and manufacturing groups is essential for determining prospective bottlenecks and implementing constant enhancements in the manufacturing workflow - Metal Stamping. By welcoming lean manufacturing concepts and leveraging modern technology advancements, manufacturers can open the full capacity of steel marking processes and accomplish higher manufacturing performance
Quality Control and Inspection Techniques
To make certain the regular manufacturing of high-quality metal stamped components, extensive quality assurance and assessment methods play a critical role in validating the accuracy and stability of the manufacturing process. Quality assurance in metal marking involves a collection of methodical checks and actions to assure that each component satisfies the specified requirements. Examination techniques such as visual exam, dimensional evaluation, and material testing are frequently employed to assess the top quality of stamped components. Visual assessments make sure the surface finish and stability of the parts, while dimensional analysis validates that the parts adhere to the called for specs. Material screening methods like solidity screening and material make-up evaluation help verify the product homes and structural honesty of the stamped components. Additionally, advanced modern technologies such as automated optical assessment systems and coordinate determining makers are progressively being utilized to boost the precision and efficiency of quality control processes in steel stamping. By implementing durable quality assurance and evaluation approaches, suppliers can maintain high criteria of high quality and uniformity in their metal stamped items.
Conclusion
Finally, steel stamping offers numerous advantages such as cost-effectiveness, accuracy, and flexibility in product advancement. By implementing style optimization techniques, choosing suitable materials, and boosting production performance, manufacturers can accomplish higher quality products with minimized preparations. Quality control and assessment approaches play a critical duty in ensuring the end products satisfy the called for criteria. On the whole, unlocking the power of metal marking requires a critical approach to improve product development procedures.
Steel stamping deals a efficient and affordable method for generating high-quality metal elements.Moreover, steel marking enables for high-volume production, making it suitable for jobs that need big their website amounts of steel components.Through careful consideration of product residential properties and geometric configurations, style optimization strategies play an essential function in improving the efficiency and capability of metal marking processes.Design optimization strategies in steel stamping processes heavily depend on strategic material choice strategies to guarantee the wanted efficiency and effectiveness of the manufactured components. The selection of material in metal stamping is critical as it directly influences the top quality, sturdiness, and general functionality of the final product.
Report this page